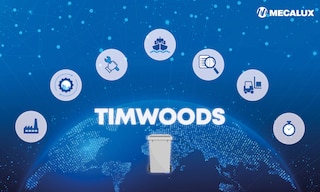
Timwoods: ¿qué es y por qué es importante para la logística?
Timwoods es una herramienta que, en el contexto empresarial, se utiliza para evitar incurrir en errores como pasos que no aportan valor, la producción excesiva, movimientos innecesarios o el desaprovechamiento del talento de los empleados. Estos se conocen como los ocho desperdicios lean.
¿Qué es ‘timwoods’ y cuál es su relación con el ‘lean’?
Timwoods se utiliza para recordar e identificar los ocho desperdicios o ineficiencias que, según el método lean, pueden darse en espacios como fábricas, almacenes, centros de distribución o, incluso, oficinas cuando el trabajo no se organiza correctamente. Prestar atención a esta metodología e integrar sus procedimientos en el plan de producción de la empresa permite agregar valor al producto o servicio final e implementar mejoras de diversas maneras.
¿Qué significa el acrónimo timwoods? Este recurso nemotécnico está compuesto por las iniciales en inglés de las palabras transporte, inventario, movimiento, espera, sobreprocesamiento, sobreproducción, defectos y habilidades. Estas siglas hacen referencia a las áreas en las que las compañías deben intervenir si desean acabar con la improductividad.
El método lean del que forma parte timwoods bebe, a su vez, de la filosofía japonesa kaizen (mejora). Se trata de una estrategia que busca recortar costes y mejorar la eficiencia de la cadena de suministro eliminando los procesos redundantes. Sus principios pueden aplicarse en la fabricación, en la gestión empresarial o en la logística.
¿Qué son los desperdicios ‘lean’?
Los desperdicios o mudas lean (del japonés muda, despilfarro) son aquellas actividades que no aportan valor y resultan de una producción o gestión deficiente, pudiendo haberse prevenido con una mejor organización. Estas ineficiencias pueden tener un efecto negativo sobre la productividad y provocar un aumento de costes, por lo que detectarlas y abordarlas es esencial para gestionar una empresa rentable.
El ingeniero industrial japonés Taiichi Ohno fue quien identificó y categorizó los desperdicios que forman el acrónimo timwoods con el fin de erradicarlos de los procesos de trabajo. Originalmente, el modelo desarrollado por Ohno resumía las siete formas de desperdiciar recursos más comunes presentes en las compañías y, más adelante, se le añadió un octavo desperdicio.
Ejemplos de ‘lean manufacturing’ en empresas
En cuanto a la producción lean o lean manufacturing, distintos clientes de Mecalux ya han incorporado sus fundamentos con éxito. La compañía austriaca ALPLA, líder mundial en soluciones de envasado, aplica la metodología lean en centros como su planta de Golborne, en el Reino Unido. Allí, utiliza transportadores y elevadores automáticos para palets para mover 2.500 de manera ágil cada día.
Igualmente, la cadena de tiendas de equipación y accesorios para motoristas Motocard coloca lo imprescindible en las estaciones de trabajo de su almacén ─un ordenador, una impresora, precinto, unas tijeras y un cúter─ a fin de que los operarios completen el mayor número de pedidos posible.
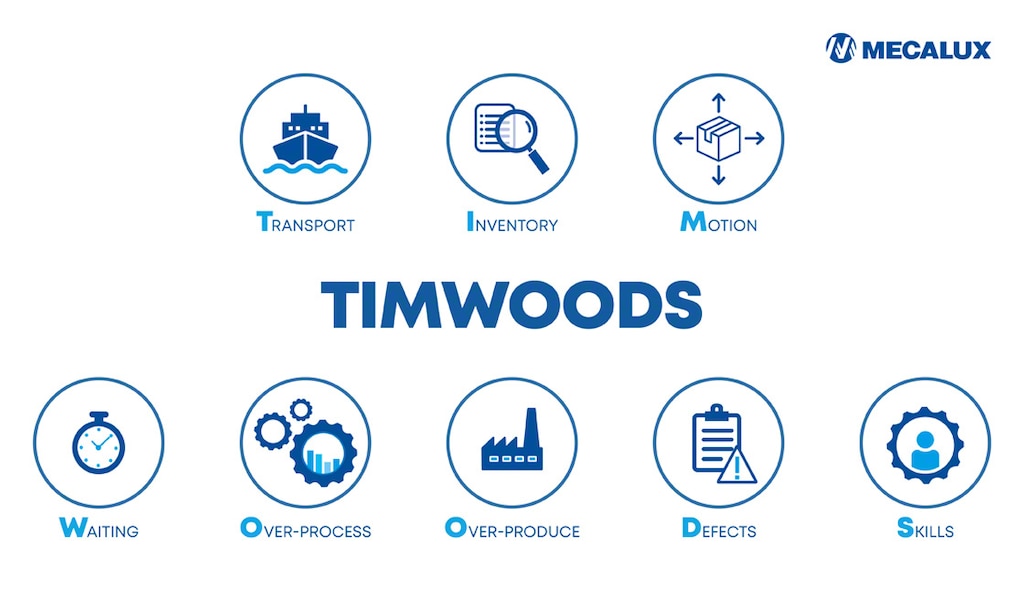
‘Timwoods’ o los 8 desperdicios ‘lean’
El listado completo de timwoods o Tim Woods funciona como una hoja de ruta para tratar de combatir las ineficiencias:
- Transport (Transporte). Trasladar los productos de un punto a otro del almacén sin un rumbo fijo o de modo injustificado supone una pérdida de tiempo y de recursos. Además, el excesivo manejo de materiales puede provocar daños o roturas y aumentar la merma de inventario.
- Inventory (Inventario). Los excesos de materias primas, productos a medio fabricar o artículos terminados que no se necesitan de inmediato afectan a la rentabilidad de las empresas al impedir dedicar el espacio de almacenaje a otros bienes.
- Motion (Movimiento). Los productos, los operarios del almacén y los aparatos de manipulación de materiales como las carretillas pueden sufrir un desgaste innecesario si se desperdician los movimientos de los camiones o las máquinas. La automatización de almacenes contribuye a minimizar este inconveniente.
- Waiting (Espera). Si son más largos de lo esperado, los períodos en que los clientes aguardan la llegada de sus artículos pueden dañar la imagen de los negocios. Asimismo, el tiempo que los productos o materias primas permanecen a la espera sin ser transportados ni procesados ocasiona pérdidas y disminuye la productividad de las compañías.
- Over-processing (Sobreprocesamiento). Consiste en llevar a cabo tareas que complican el flujo de trabajo y no aportan valor al bien o servicio final. Algunas están relacionadas con la generación de documentación superflua, una separación de funciones poco clara o cuestiones como mantener registros dobles.
- Over-production (Sobreproducción). Fabricar más de lo necesario puede ser un error y provocar sobrestock, es decir, una acumulación de productos o materias primas en las instalaciones. Lo mejor para evitarlo es contar con una buena previsión de la demanda, métodos de trabajo optimizados y herramientas como sistemas de almacenaje adecuados o un SGA.
- Defects (Defectos). Fabricar productos imperfectos afecta negativamente a la satisfacción de los usuarios y genera otros costes como los asociados con la logística inversa, los reembolsos o las reposiciones.
- Skills (Habilidades). Si te preguntabas cuál es el octavo desperdicio que se incorporó al listado de Ohno, este se centra en el capital humano de la empresa. Y es que no sacar el máximo provecho a los conocimientos, la creatividad y las habilidades de los empleados es todo un desperdicio. Es por ello que se aconseja involucrar al personal de todos los niveles para que aporte ideas de mejora y más información destinada a la resolución de problemas.
Ejemplos de desperdicios ‘lean’ o ‘timwoods’
En el almacén pueden darse algunos desperdicios timwoods. Por ejemplo, contar con líneas de producción o layouts mal diseñados y procesos excesivamente complejos genera un desperdicio vinculado al transporte (T). Una previsión de la demanda deficiente y la ausencia de un software de gestión de inventarios pueden complicar el inventario (I), y los sistemas de almacenaje poco óptimos o mal conectados con las líneas de producción pueden provocar retrasos y esperas (W). A su vez, levantar elementos pesados por una ausencia de equipos como carretillas o tener que desplazarse para entregar documentación desaprovecha las energías del personal y contribuye a un desperdicio relacionado con el movimiento (M).
Eliminar los ‘timwoods’ en ‘lean manufacturing’
Mantener un inventario permanente automatiza el control de entradas y salidas de stock y previene su obsolescencia. Las compañías con actividades logísticas pueden controlar y optimizar todos los procesos y recursos de sus sistemas automáticos o manuales con el software de gestión de almacenes (SGA) Easy WMS. Diseñado para dirigir instalaciones de mediano y gran tamaño, garantiza la trazabilidad total y en tiempo real del stock, reduce drásticamente los errores y potencia la productividad, lo que asegura un rápido retorno de la inversión. Contacta con nosotros para que desde Mecalux te asesoremos sobre esta y otras soluciones de logística y almacenaje.