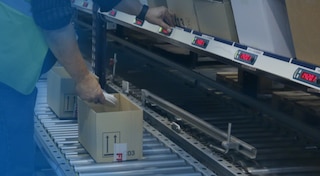
El método Poka-Yoke explicado en 5 ejemplos
El Poka-Yoke es una técnica de mejora continua que tiene dos objetivos fundamentales: por un lado, evitar errores inadvertidos en los procesos de producción y logísticos y, por el otro, corregir las ineficiencias en el supuesto de que lleguen a producirse.
En la actualidad, la omnicanalidad ha obligado a las empresas a preparar y entregar en el menor tiempo posible un número muy elevado de pedidos diarios. En este escenario, los responsables de los almacenes se esfuerzan en eliminar posibles fallos que suponen demoras y pérdida de confianza de los clientes.
Pero, ¿cómo el Poka-Yoke ayuda a suprimir los errores en el picking? En este artículo veremos en qué consiste exactamente y lo ilustraremos con cinco ejemplos de cómo puede aplicarse.
¿Qué es el Poka-Yoke?
Creado en la fábrica de Toyota en Japón en 1960, el método Poka-Yoke se traduce, literalmente, como “a prueba de errores”. Se trata de una técnica de mejora continua dedicada a evitar equivocaciones en cualquier proceso de producción y logístico.
El Poka-Yoke puede englobar estrategias que perfeccionen y optimicen los procedimientos de un almacén o una planta de producción como, por ejemplo, las 5S del método Kaizen.
También puede hacer referencia a objetos diseñados específicamente para anticiparse a los errores humanos como los cables USB, utilizados para transmitir datos y cargar dispositivos. Estos solo pueden introducirse en el puerto por la cara adecuada pues, de lo contrario, no cumplirán su función.
El ingeniero Shigeo Shingo desarrolló esta filosofía de trabajo con el propósito de eliminar las ineficiencias en los procesos de producción y su puesta en práctica fue todo un éxito. Lo logró aplicando prácticas que simplifican el trabajo de los operarios y que minimizan las distracciones para que puedan concentrarse en sus tareas.
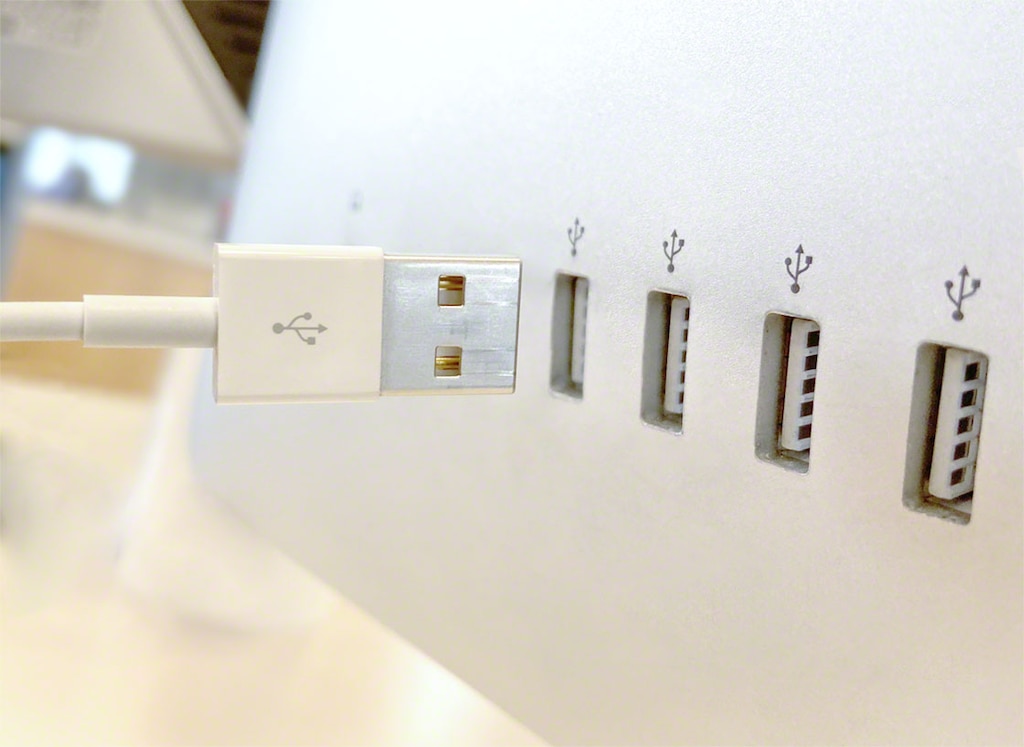
¿Cómo aplicar el Poka-Yoke?
La pregunta clave es: ¿cómo adoptar el Poka-Yoke, por ejemplo, en una planta de producción o en un almacén? Para empezar, lo primero que hay que hacer es identificar y examinar cada uno de los procesos. En este análisis, se estudia la forma en la que se desarrolla cada operativa, haciendo especial hincapié en los posibles fallos que se puedan cometer.
A continuación, se escoge el enfoque Poka-Yoke adecuado, es decir, se plantea una solución que minimice o impida todos los posibles fallos. También se asume que hay errores inevitables y, para estos casos, se diseña un sistema de detección y reacción, con el fin de reducir su impacto.
Por último, se hace un seguimiento de la operativa con el objetivo de constatar que el Poka-Yoke y su implementación han funcionado.
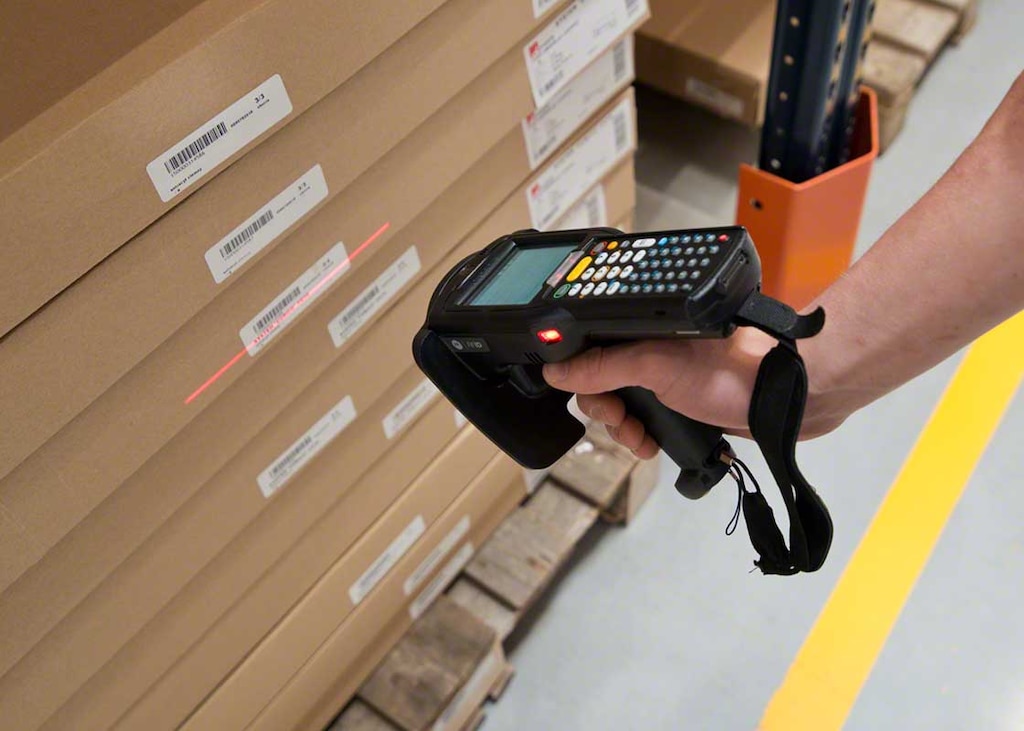
Tipos de Poka-Yoke
El Poka-Yoke puede clasificarse en cuatro tipos:
- Secuencial. Se basa en preservar un orden o una secuencia de un proceso. Si no se cumple, no se puede cerrar la tarea y, por tanto, es imposible avanzar hasta el siguiente proceso.
- Informativo. La información clara, sencilla y directa ayuda a los operarios a realizar las distintas operativas sin equivocarse.
- Agrupado. Consiste en preparar kits con todos los materiales y piezas necesarias para llevar a cabo una operación. De esta forma, los operarios no pierden tiempo en ir a buscar los materiales que necesitan para trabajar porque ya los tienen todos a mano.
- Físico. Son cambios en la usabilidad de ciertos dispositivos con la intención de prevenir errores. Por ejemplo, las lavadoras o los microondas que utilizamos en casa no se ponen en funcionamiento hasta que las puertas no estén debidamente cerradas o se haya seguido una cierta secuencia (elegir temperatura, minutos, programa, etc.).
Con todas estas prácticas lo que se busca verdaderamente es eliminar los errores en las actividades repetitivas o en aquellos procesos donde los operarios pueden equivocarse por desconocimiento o despiste. Así, los operarios pueden centrarse en su trabajo, en vez de malgastar el tiempo en hacer comprobaciones o en corregir las ineficiencias.
Cinco ejemplos de Poka-Yoke centrados en la logística
En realidad, no existen reglas fijas a la hora de diseñar un Poka-Yoke. Las prácticas que se apliquen o los objetos que se utilicen para eliminar equivocaciones dependerán del ingenio de las personas implicadas en cada proceso.
Acto seguido, veremos a través de algunos ejemplos qué prácticas Poka-Yoke son las que se suelen emplear de manera más frecuente en un almacén. En el sector logístico, el Poka-Yoke forma parte de lo que se conoce como Lean logistics, es decir, un modo de trabajo destinado a potenciar aquellos procesos logísticos que aportan valor con el fin de disminuir costes.
Ejemplo 1: Poka-Yoke secuencial con un software de almacén
Un software de gestión de almacén (SGA), como es Easy WMS de Mecalux, es un programa capaz de optimizar las operativas y de guiar a los operarios para que cumplan sus tareas de la forma más rápida y eficiente posible.
El SGA puede actuar como un Poka-Yoke secuencial, pues los operarios, a través de los terminales de radiofrecuencia, siguen las indicaciones del SGA una tras otra. Este sistema les muestra qué hacer paso a paso y los operarios deben confirmar que han realizado cada acción para recibir más órdenes.
Ejemplo 2: Poka-Yoke informativo con indicadores ‘pick-to-light’
La preparación de pedidos es una de las operativas del almacén con un mayor riesgo de incurrir en equivocaciones. El cansancio físico de los operarios, la semejanza de los productos o la similitud de las estanterías pueden conllevar errores (pedidos a los que les falten artículos, pedidos con artículos erróneos o con la cantidad incorrecta, etc.).
Una solución para evitar fallos en el picking es recurrir a los dispositivos luminosos pick-to-light. Esta tecnología, que entraría dentro del Poka-Yoke informativo, indica de manera visual y evidente los productos que hay que recoger y en qué cantidad. Su verdadera función es dirigir el trabajo de los operarios hacia el “no-error”.
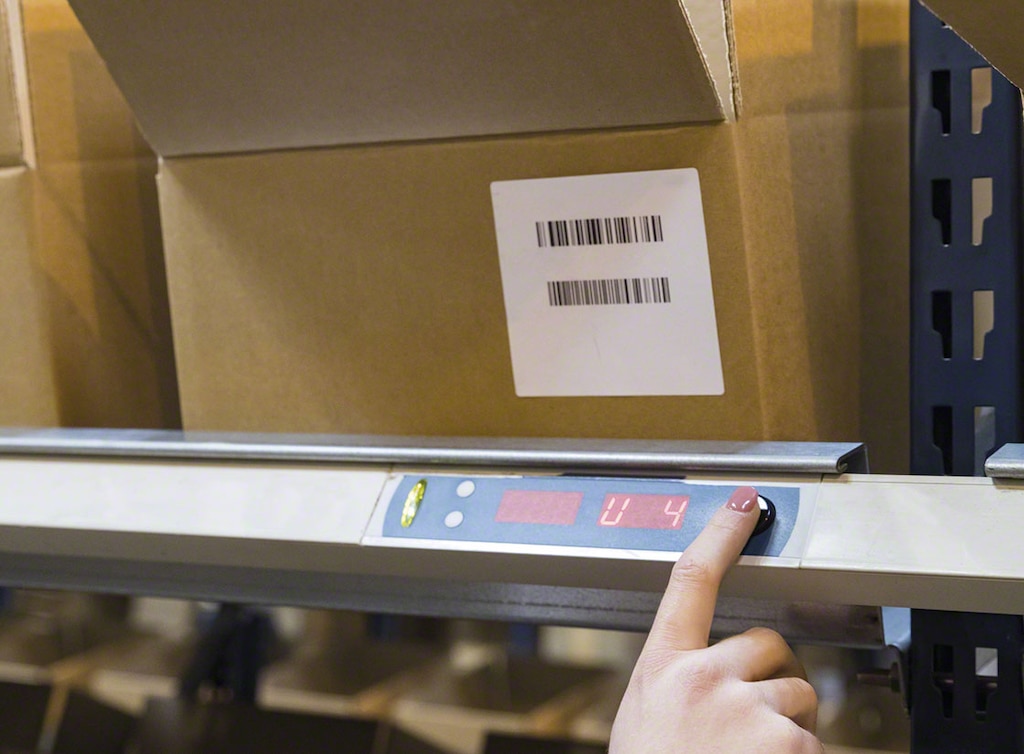
Ejemplo 3: Poka-Yoke agrupado en operativas de ‘kitting’
En muchos almacenes se hace kitting: un proceso que consiste en reunir las partes individuales que conforman un producto y crear un paquete con ellas para que otros operarios compongan el artículo final.
Esto sería un Poka-Yoke agrupado, porque, en los puestos de montaje, los operarios disponen de todos los materiales necesarios para elaborar el producto y no tienen que recorrer el almacén localizando los distintos componentes.
Preparar los kits con antelación proporciona agilidad y precisión. Se empieza a preparar un artículo hasta que estén reunidos todos los componentes.
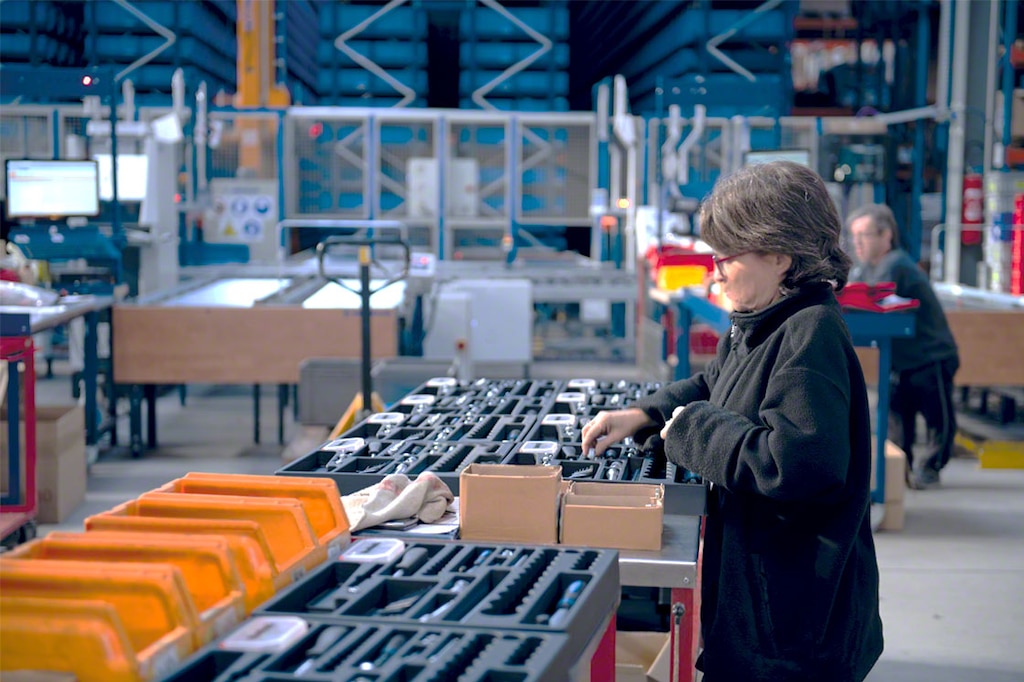
Ejemplo 4: Poka-Yoke físico gracias a los cerramientos de seguridad
El Poka-Yoke físico más corriente en un almacén se basa en los cerramientos de seguridad. Más que prevenir errores, su función primordial es evitar accidentes.
Las áreas donde operan equipos de manutención automáticos como transelevadores están preservadas para evitar el acceso de personal no autorizado. En el momento en que una persona cruza estos cerramientos y accede en la zona de trabajo de un transelevador ─ya sea para realizar tareas de mantenimiento o por equivocación─, la máquina se detiene.
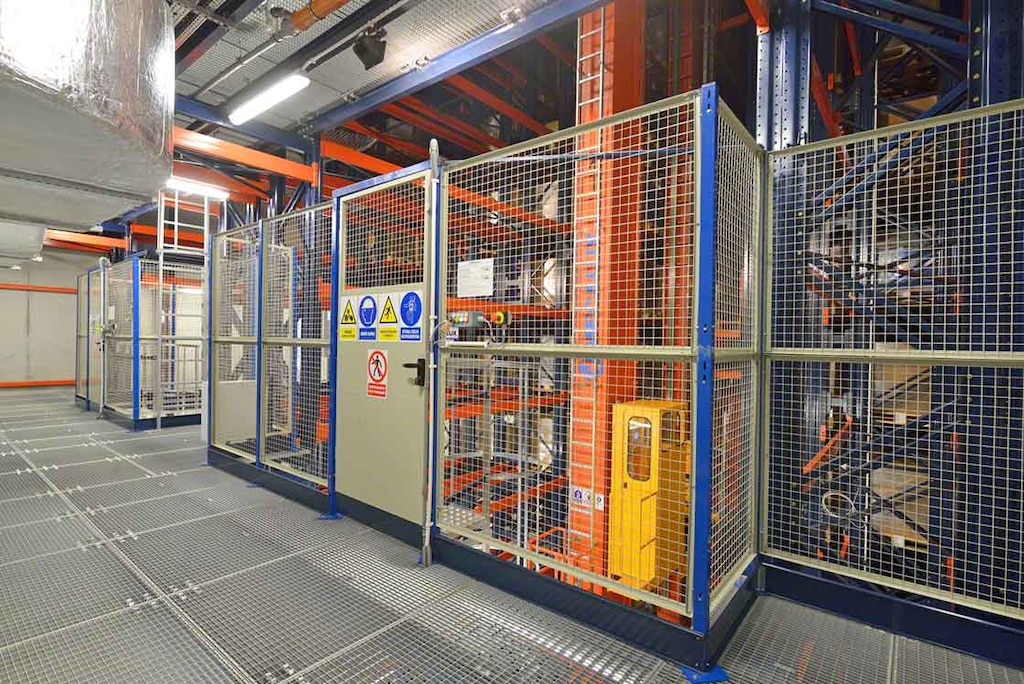
Ejemplo 5: Poke-Yoke físico usando carros de picking
Otro Poka-Yoke físico habitual en los almacenes son los carros para preparar pedidos. Estos suelen tener unas dimensiones concretas en función del tamaño de los productos y de los pedidos.
Si en un almacén se hace picking por olas o wave picking, además, estos carros se dividen en tantas ubicaciones como pedidos tenga la ola. De esta manera, cada ubicación corresponde a un pedido, lo que evita equivocaciones.
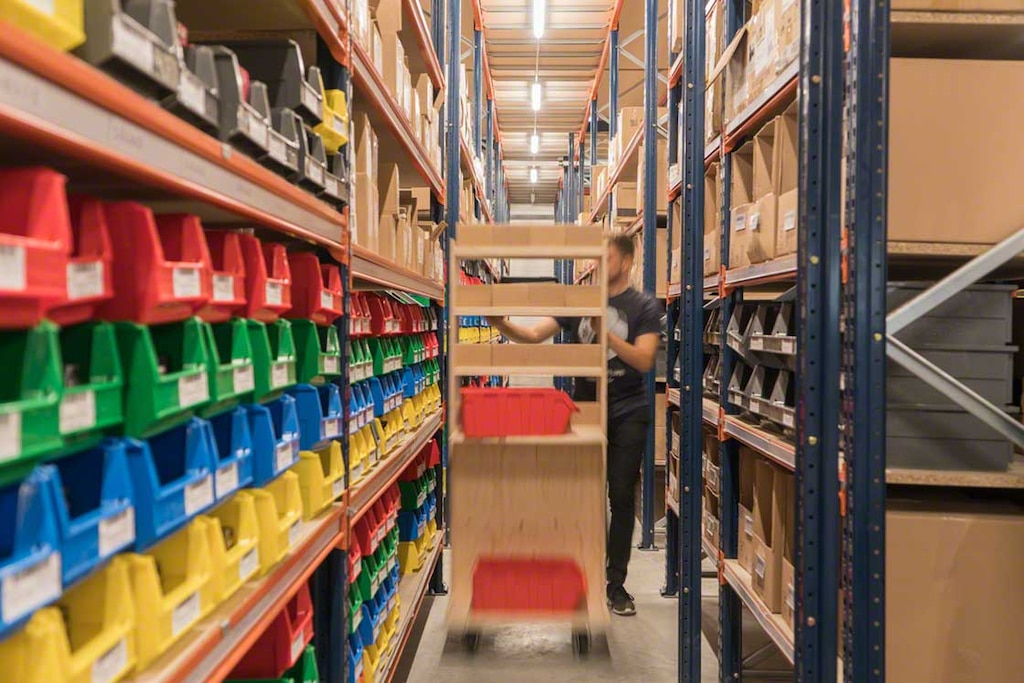
Eliminar errores, potenciar la calidad
El Poka-Yoke consiste en aplicar técnicas que eviten errores, sobre todo en aquellas actividades más repetitivas. Hemos podido comprobar cómo forma parte de nuestro día a día, con objetos y aparatos que empleamos en nuestra vida cotidiana, así como en almacenes y plantas de producción.
El Poka-Yoke tiene como objetivo elevar la calidad de los procesos y, por consiguiente, del servicio y del producto final. De ese modo, además, se obtiene una mayor satisfacción por parte de los clientes.
En Mecalux disponemos de una larga experiencia desarrollando sistemas de almacenaje que pueden simplificar las operativas de tu almacén y ayudarte a lograr un mayor rendimiento. Contacta con nosotros para que diseñemos contigo un almacén eficiente, preparado para evitar cualquier posibilidad de cometer errores.