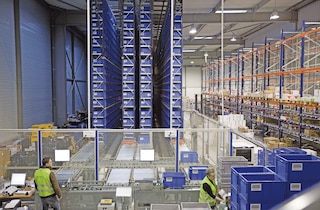
Cómo optimizar la logística de producción
La logística de producción ha sido, tradicionalmente, un sector lineal y previsible. Durante años, los fabricantes representaban el eslabón situado entre los proveedores de materias primas y los distribuidores. Sin embargo, la realidad económica actual ha roto esa tendencia y ha obligado a las compañías a hacer frente a procesos de fabricación personalizados con un stock de materiales tan numeroso como heterogéneo.
Tendencias empresariales como el just-in-time, la internacionalización de los mercados y las exigentes demandas de los clientes en cuanto a la rapidez de entregas están impulsando la transformación de la logística de producción. En este artículo, definimos y ponemos en valor las características del nuevo paradigma de logística de producción y desciframos las mejores estrategias para optimizarla.
¿Qué es la logística de producción?
La logística de producción o logística industrial engloba la gestión y optimización de los procesos de almacenamiento, así como el movimiento de materiales en las instalaciones ligadas a un centro de fabricación. En definitiva, abarca todos los procesos logísticos que se dan desde la compra de materias primas hasta la creación del producto.
Radiografía de los procesos de producción
Para entender mejor el funcionamiento de la logística de producción, vamos a repasar brevemente los dos sistemas de fabricación más habituales y el papel que representa cada uno de ellos:
- Fabricación para stock o sistema ‘push’
Tiene lugar cuando el producto final responde a una amplia demanda y cuenta con características estándares que no incluyen ninguna personalización. En este caso, las fábricas manufacturan por adelantado los artículos. Estos pasan directamente al almacén y, por tanto, el departamento comercial únicamente vende el stock disponible en almacén (a diferencia del sistema pull, que veremos a continuación).
- Fabricación sobre pedido o sistema ‘pull’
El sistema pull funciona al revés: la fábrica produce una vez recibe los pedidos de los clientes, a los que se les da una fecha de entrega establecida. Con este método, aunque no haya stocks de producto terminado, sí que la empresa puede mantener inventarios de productos semielaborados, ya que estos permiten acortar los tiempos de entrega una vez el pedido del cliente se ha efectuado.
A pesar de que hay sectores que destacan por usar un sistema de fabricación u otro, en la realidad ambos pueden convivir. Por ejemplo, en el caso del sector automovilístico, se fabrican vehículos estándar (sistema push), pero también otros bajo demanda con características personalizadas (sistema pull).
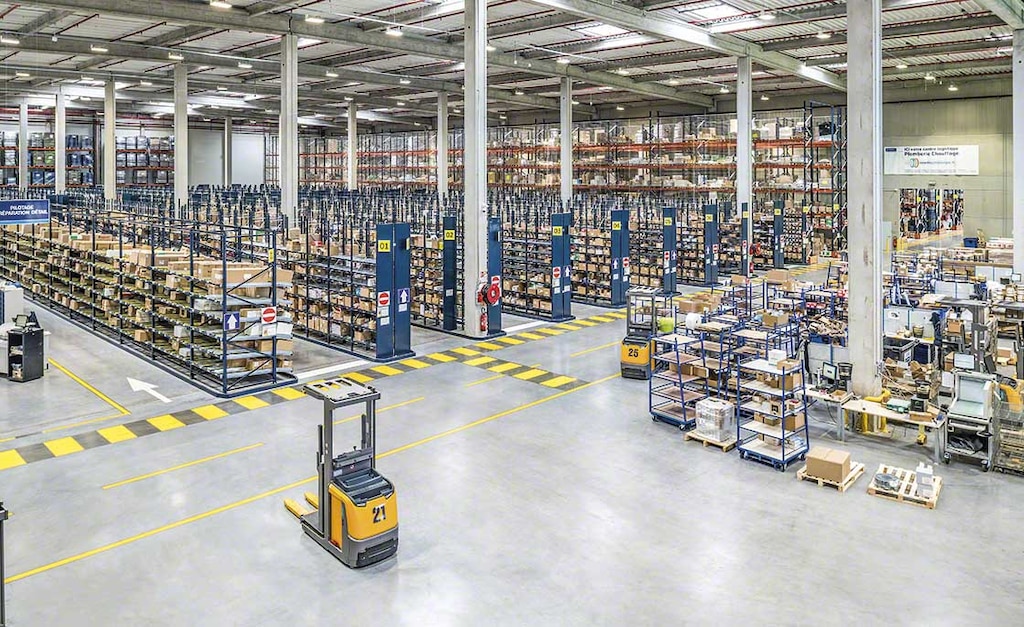
La relación entre producción y logística en la industria
La labor de la logística de producción es reducir el lead time de fabricación, es decir, el tiempo que discurre desde que se genera una orden de trabajo hasta que el producto está terminado.
De hecho, para acortar los tiempos de producción, muchas empresas industriales están optando por proveedores locales de materiales y componentes. Esta tendencia ha revertido parcialmente la deslocalización de compañías: por ejemplo, según Industry Week, en 2018 aumentó un 38% las empresas manufactureras que se instalaron en Estados Unidos.
Otro factor crucial en la logística de producción es la propia gestión de stock, fundamental para acometer una fabricación más rápida. Para ello, el almacén tiene que ser capaz de gestionar eficazmente los dos tipos de demanda que afectan a la logística de producción: la demanda de los clientes finales, ya esté basada en previsiones de ventas o en pedidos solicitados a fábrica (es la demanda independiente del proceso productivo), y la demanda de la fábrica, que solicita al almacén todas las materias primas que se precisan para crear el producto final (es la demanda dependiente del proceso de fabricación).
En relación con este concepto de demanda de fábrica, la empresa manufacturera es capaz de calcular a ciencia cierta qué materias primas necesita la planta de producción para elaborar cada producto. Aquí conviene introducir los conceptos de BOM (Bill of Materials) y de sistema MRP (Materials Requirement Planning). El BOM hace referencia al inventario o listado de componentes requeridos para la fabricación de los productos, mientras que el sistema MRP es el software informático que determina qué materiales se necesitan y en qué cantidad para fabricar cierto modelo.
Coordinar las áreas de producción y de logística pasa, por tanto, por controlar estos dos tipos de demanda (la dependiente e independiente del proceso productivo) y organizar los almacenes industriales en función de cada una. Las instalaciones de almacenaje vinculadas a plantas productivas pueden albergar productos terminados, componentes o materias primas que surten al proceso productivo o bien piezas y recambios para el servicio posventa.
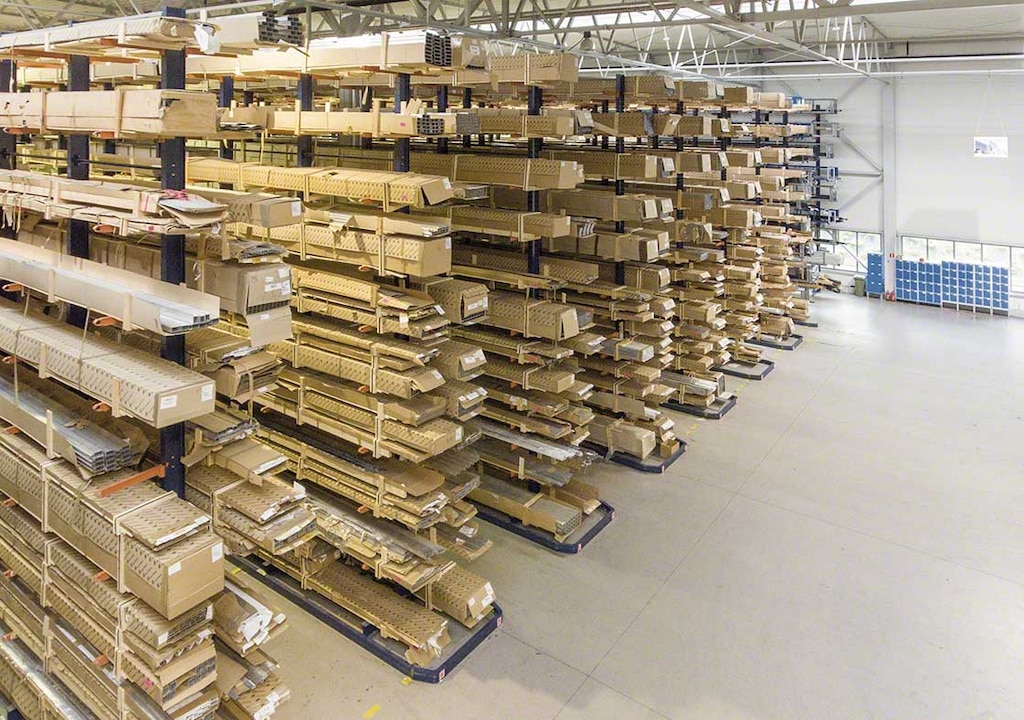
Cómo optimizar el almacén dedicado a la logística industrial
Aplicando un enfoque de Lean logistics, que parte de la filosofía del Lean manufacturing, una logística de producción efectiva se basa en reducir aquellas operaciones que no añaden valor al producto. Ejemplos de ello son el transporte interno, las colas o esperas entre procesos, los stocks de trabajo en curso, entre otros.
El objetivo final es conseguir ofrecer un mejor servicio y un recorte de costes en general. Pero, ¿cómo lograrlo entonces?
- Automatización a medida del proceso productivo
Cuando los almacenes sirven como depósito de stock que llega directamente desde producción, deben estar preparados para dar cabida y mover gran cantidad de mercancías, generalmente palets. La automatización del transporte de materiales es una solución muy utilizada al tratarse de procesos repetitivos y cargas pesadas. Además, gracias a ella se logra la optimización del espacio y una mejora en la productividad de la instalación al reducirse drásticamente las incidencias en el manejo de mercancías.
No obstante, también hay almacenes de piezas y recambios dedicados a la logística industrial cuya operativa está centrada en la preparación de los pedidos que surten a líneas de producción. Al tratarse habitualmente de inventarios muy heterogéneos y de unidades de carga de pequeño tamaño, una de las estrategias más comunes se basa en zonificar el almacén en función del método de rotación ABC y automatizar el movimiento de materiales con transportadores de rodillos para conectar las distintas áreas.
- Software para la gestión de los procesos en logística de producción
Los SGA para producción añaden a las funcionalidades base de un software de gestión de almacenes otras especialmente orientadas a optimizar el área manufacturera. Estos programas, que en cierto sentido operan como sistemas MRP, controlan y coordinan la relación que se da entre la demanda de los clientes y la demanda dependiente del proceso productivo.
Los sistemas de gestión del almacén se han revelado, así, como una herramienta esencial para tener una visión global del inventario ligado a las tareas de producción. Contar con un SGA especializado en producción facilita:
- La clasificación por tipos de stock: en logística de producción, pueden ser de materia prima, de trabajo en curso o semielaborados o existencias de productos terminados.
- Visualizar el stock en tiempo real: el software garantiza el conocimiento del número y del estado de la mercancía en todo momento.
- Producir según el método just-in-time: este método sería imposible de aplicar sin una gestión automatizada del almacén.
La importancia de la integración en logística de producción
En la actualidad, la industria se encuentra ante un panorama de fabricación flexible y diversificado, en el que ofrecer un servicio eficaz al cliente depende del correcto engranaje de la logística de producción. Ante este paradigma, la automatización y la implementación de SGA especializados en procesos de fabricación son dos estrategias clave para optimizar la logística de producción. Si quieres conocer más en profundidad cómo hacer más eficiente la logística industrial de tu empresa, te invitamos a contactar con nosotros y uno de nuestros expertos analizará la situación y propondrá mejoras para tus instalaciones.